The recent economic down turn the world over has neccessitated Lean thinking in every aspect of our working.
“Lean” simply means a systematic approach to identiying all types of wastes and optimum utilization of resources, continuous improvement, ensuring smooth flow of the product in the supply and manufacturing chain and meeting customers demand satisfaction.
In short “Lean” is about doing more with less inventory, less time, less space, less movement people, less mony.
Lean is the speed with which you can deliver a quality product or service by “doing a job right first time”
Lean Thinking:
Every entity of this world is created twice; first in human mind in the form of ‘thought’, and second; the manifestation of thought into the ‘physical form’. To create a lean enterprise people have to begin with lean thinking.
Lean Thinking is a highly evolued method of managing an organization to improve the productivity efficiency, effectiveness, speed and quality of its products and services.
Lean is…. mindset, or way of thinking, with a commitmet to achieve a totally waste free operation that is focused on a customer purpose. It is achieved by simplifying and continuously improving all processes in a corporate culture of trust, respect and full employee involvement. It is about customer purpose, process, people, simplicity, flow, visibility, partnership, and value creation for customer wealth generation for the organization.
Lean is from an operations perspective… Lean production cuts costs & inventories rapidly to free cash,which is critical in a business economy. It also supports growth by improving productivity and quality, reducing lead times and freeing huge amount of resources.
In other words, we should evolve “Lean Quality Circle” with minimum number of people and, to start with, it can be started with as even “dyad” (two) or “Traid” (three) with scope for additions to it according to the needs and the type of projects and knowledge and skills required. The maximum limit will be only FIVE members.
The Scope covers formation of Lean Quality Circle.
Scope:
To cater to the needs of experienced Quality Circle members to turn out large number of small projects to meet company’s objective / Goal in a short time with DMAIC approach; this approach can be informed without structured meetings.
Structure:
Minimum 2 persons can be core members as Leader & Dy.Leader. They can coopt other members depending upon the nature of the problem. The concerned Executive will act as Faciliator.
Frequency Of Meeting:
There will not be fixed regular formal meetings. Meetings will be informal and at the place / equipment where the problem exists. Frequency of the meeting will depend upon the decision of the group members as and when required. Weekly progress reports will be noted by Leader or Dy.Leader in the meeting register.
Selection Of Problem:
The Problems can be taken from already identified problems / problem Bank based on Management Goals / Objectives. Problem may be taken from the current priority problem of their work areas decided by the group member. After selecting the problem, the same has to registered with the oordinator and obtain reistration number.
Problem Solving Technique:
DMAIC procedure will be adopted and the presentation also can be made accordingly.
Presentation at Conventions:
In CCQC, NCQC & ICQCC, it will be treated as a Special Case Study and evaluated accordingly. However the final format should present the brief details of the project.
Team Introduction
Project Title
Objective Goal
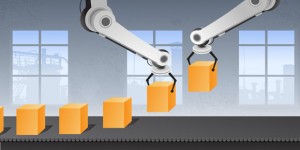